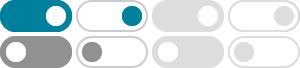
Isotropic etching - Wikipedia
In semiconductor manufacturing, isotropic etching is a method commonly used to remove material from a substrate via a chemical process using an etchant substance. The etchant may be in liquid-, gas- or plasma-phase, [1] although liquid etchants such as buffered hydrofluoric acid (BHF) for silicon dioxide etching are more often
Anisotropic Etching vs. Isotropic Etching - Thierry Corp
In contrast to isotropic etching, which produces a lower resolution concave shape under the photoresist etching mask, anisotropic etching removes material in specific directions enabling the production of geometric characteristics such as sharp corners, flat surfaces, and deep cavities.
For isotropic wet etching, a mixture of hydrofluoric acid, nitric acid, and acetic acid (HNA) is the most common etchant solvent for silicon. The concentrations of each etchant determines the etch rate. Silicon dioxide or silicon nitride is usually used as a masking material against HNA.
Isotropic Etching - SpringerLink
Isotropic etching results in equal etch rates in all directions. An undercutting of the resist edges in the dimension of the film thickness is always observed. The isotropic character of etch processes makes it impossible to generate openings with high aspect ratios.
Isotropic vs Anisotropic Etching: Complete Guide
Mar 28, 2025 · Isotropic etching removes material uniformly in all directions, producing rounded or undercut features, while anisotropic etching is highly directional, creating well-defined structures essential for semiconductor and MEMS fabrication.
Isotropic Etching to Anisotropic Etching - Cadence PCB Design
Jun 3, 2020 · Isotropic etching applies uniform amounts of etching in all directions and at the same rate. The term “isotropic” derives from the Greek “iso” for “equal” and “tropos” for “a turn.” While proceeding in all directions, isotropic etching removes more material at the top edge than at the bottom edge.
Isotropic and Anisotropic Silicon Wet Etching Processes
May 23, 2023 · Etching Mechanisms: Isotropic etching involves removing material in all directions at an equal rate, creating a rounded profile. Meanwhile, anisotropic etching removes material along specific crystallographic planes, producing sharp corners and edges.
Isotropic etch processes are rate controlled either by transport processes with direction-independent transport rate (most frequent case of isotropic etching) or by surface processes in the case of removing completely isotropic built materials.
Isotropic Etching and Anisotropic Etching of Silicon Wafer
Jul 1, 2022 · Isotropic etching is more difficult to control than anisotropic etching, but it is faster. During the initial stages of silicon wafer fabrication, large features are etched into the silicon. At this stage of fabrication, etch rate is important to facility throughput.
Wet etching is a process in which chemical solutions, or etchants, are used to dissolve areas of a silicon substrate that are unprotected by an etching mask. The two different types of wet etching are isotropic and anisotropic etching.